1. Site Preparation
- Survey and Design:Begin with a comprehensive site survey to evaluate the slope or wall. Based on the soil conditions, a design is developed specifying the required length, diameter, spacing, and inclination of the anchor bolts.
- Excavation:Excavation is performed in stages, typically 1 to 2 meters deep at a time, to maintain stability during the process.
2. Drilling Holes for Anchor Bolts
- Drilling Holes:Horizontal or slightly inclined holes (usually 10 to 20 degrees from horizontal) are drilled into the soil or rock mass. Hole diameters typically range from 75 mm to 150 mm, depending on the design specifications.
- Hole Length:The length of the holes depends on the depth requirements for the anchor bolts, generally ranging from 3 to 10 meters.
3. Inserting the Anchor Bolt
- Steel Anchor Bolt:Steel bars, typically with diameters of 25 to 40 mm, are inserted into the pre-drilled holes. These bars are often ribbed or deformed to improve bonding with the grout.
- Corrosion Protection:For added durability, the steel bars are often coated with a corrosion-resistant material such as galvanization or epoxy coatings. In more aggressive environments, double corrosion protection is recommended.
4. Grouting the Anchor Bolt
- Grout Injection: Grout, typically cement-based, is injected into the hole to bond the steel bars to the surrounding soil or rock. The grout is pumped under pressure to ensure it fully encapsulates the anchor and creates a strong bond.
- Grouting Techniques:Two common grouting techniques are employed:
- Gravity Grouting:Used primarily for stable soils, relying on gravity to inject the grout.
- Pressure Grouting: Grout is pumped under pressure for better contact and greater strength.
5. Facing Installation
- Temporary Facing:A temporary facing, such as shotcrete, wire mesh, or steel plates, is applied to maintain the stability of the structure during construction. Shotcrete is often sprayed onto the excavated surface and anchor bolts for immediate support.
- Permanent Facing:Once the anchor bolts are fully installed and stabilized, a permanent facing is applied (shotcrete, cast-in-place concrete, or precast panels) to provide long-term protection and stability.
6. Drainage Installation
Drainage Provisions: Drainage systems, such as weep holes or drainage mats, are installed behind the facing to manage water accumulation. This is crucial as excessive water pressure can reduce the effectiveness of the anchor bolts.
7. Monitoring and Testing
7.1 Pullout Tests: To ensure that the anchor bolts meet the design strength requirements, pullout tests are performed on select bolts.
7.2 Ultrasonic Nail Integrity Tester:
To enhance the monitoring process, we recommend the use of an Ultrasonic Anchor Bolt Tester, a non-destructive testing solution designed to evaluate the quality and integrity of anchor bolts.
7.2.1 Principle:
The tester operates based on ultrasonic wave propagation. High-frequency waves are introduced into the anchor bolt, and the reflected signals are analyzed to determine the bolt’s length, identify internal defects (such as cracks or voids), and assess the bonding quality between the bolt and the surrounding material.
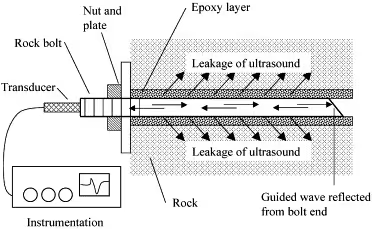
7.2.2 Testing Process:
- Preparation: The transducer is securely coupled to the exposed surface of the anchor bolt with a coupling agent to ensure optimal wave transmission. Calibration is done to match the material properties and test conditions.
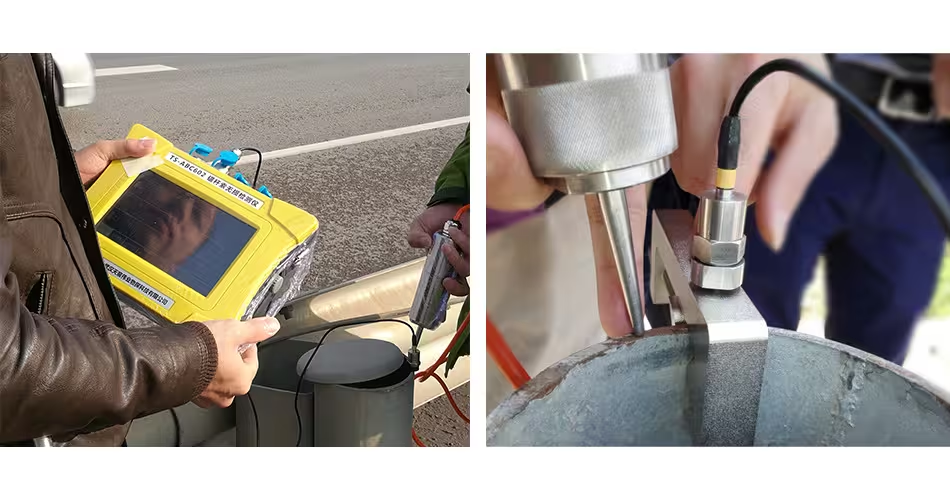
- Ultrasound Transmission: Ultrasonic waves are transmitted through the bolt, interacting with its internal structure and the interface with the surrounding material.
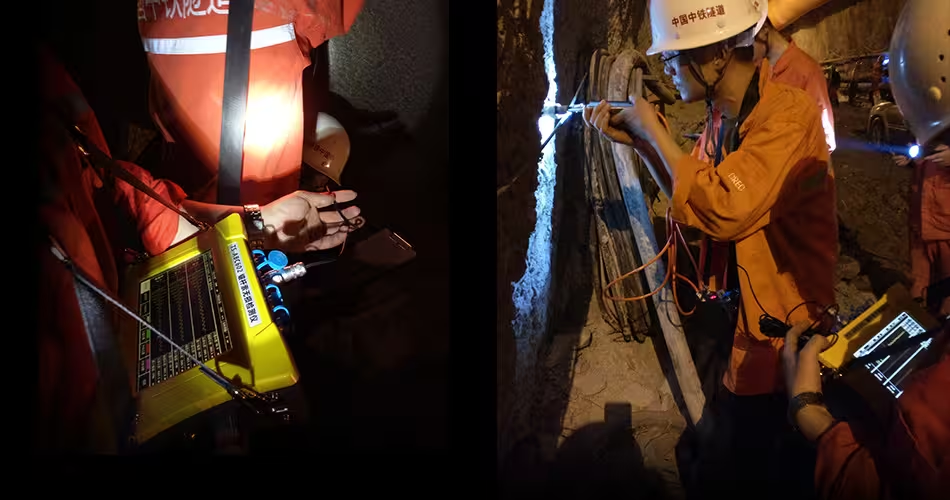
- Signal Reception: Reflected signals are captured and analyzed, revealing any defects or discontinuities.
- Data Processing: The tester calculates the time of flight (TOF) and signal amplitude to assess the bolt’s length and identify potential issues such as cracks, voids, or weak bonding.
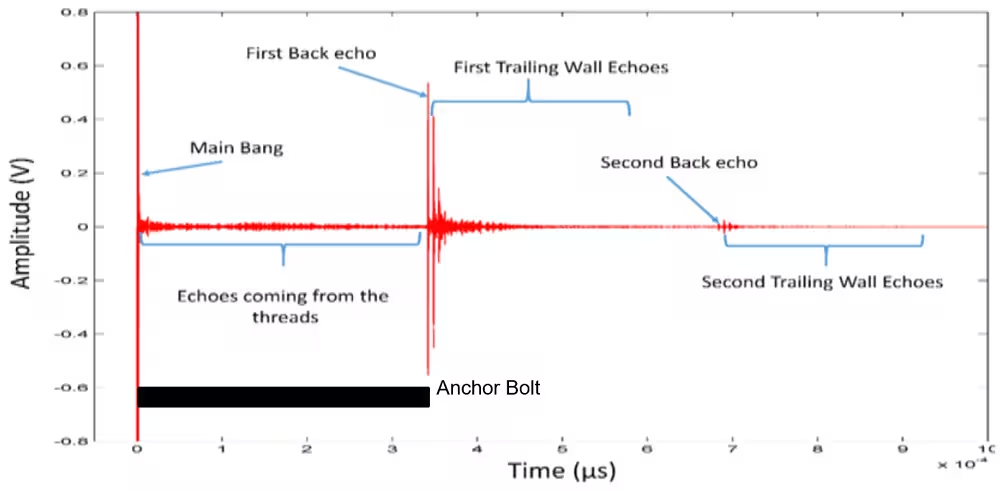
- Analysis and Reporting: Results are displayed on the device or transferred to analysis software for detailed interpretation. The system provides quantitative data to evaluate the integrity and anchorage of the bolts.
7.3 Monitoring:
Continuously monitor the wall or slope for movement and stress on the anchor bolts during and after construction.
8. Final Finishing
Finishing: After the anchor bolts and facing are installed and the structure is stabilized, finishing treatments are applied. This may include protective coatings, paint, or landscaping to improve aesthetics and provide additional protection.
By incorporating the Ultrasonic Anchor Bolt Tester into the testing phase, the entire anchor bolt installation process becomes more reliable and efficient. This NDT solution not only ensures the quality of the installation but also contributes to long-term safety and performance.